Part One of Our Ultimate Guide to Modern Supply Chain Management
Welcome to part one of our Ultimate Guide to Modern Supply Chain Management! In this blog series, we’ll dive deep into the intricacies of building, optimizing, and streamlining your supply chain. The goal is to make the lives of those working in the supply chain management trenches much easier, empowering them to boost supply chain efficiency and effectiveness.
In the first installment of our series, we guide you through the process of conducting an internal supply chain audit. We’ve already covered the importance of regularly conducting external audits — or audits of your suppliers — and we’ve previously detailed how to conduct an external supply chain audit.
But it’s equally important to examine the quality of your internal supply chain processes so you can learn more about the health of your supply chain and identify areas for improvement and growth. In this blog, we’ll cover:
- Steps to take before you conduct an audit
- The value of supply chain management software when conducting a supply chain audit
- Supply chain risks you need to watch out for
- Internal audit process steps including the most important supply chain data to analyze
Keep reading to learn how to effectively conduct an internal supply chain audit.
Important Steps Before You Conduct Your Audit
Conducting an internal supply chain audit is a huge task. If your team isn’t organized, it could lead to a messy and ultimately futile audit. To ensure success, it’s important to carry out a few planning steps before you even begin your audit.
Here are the planning and strategic steps you’ll want to perform before you start:
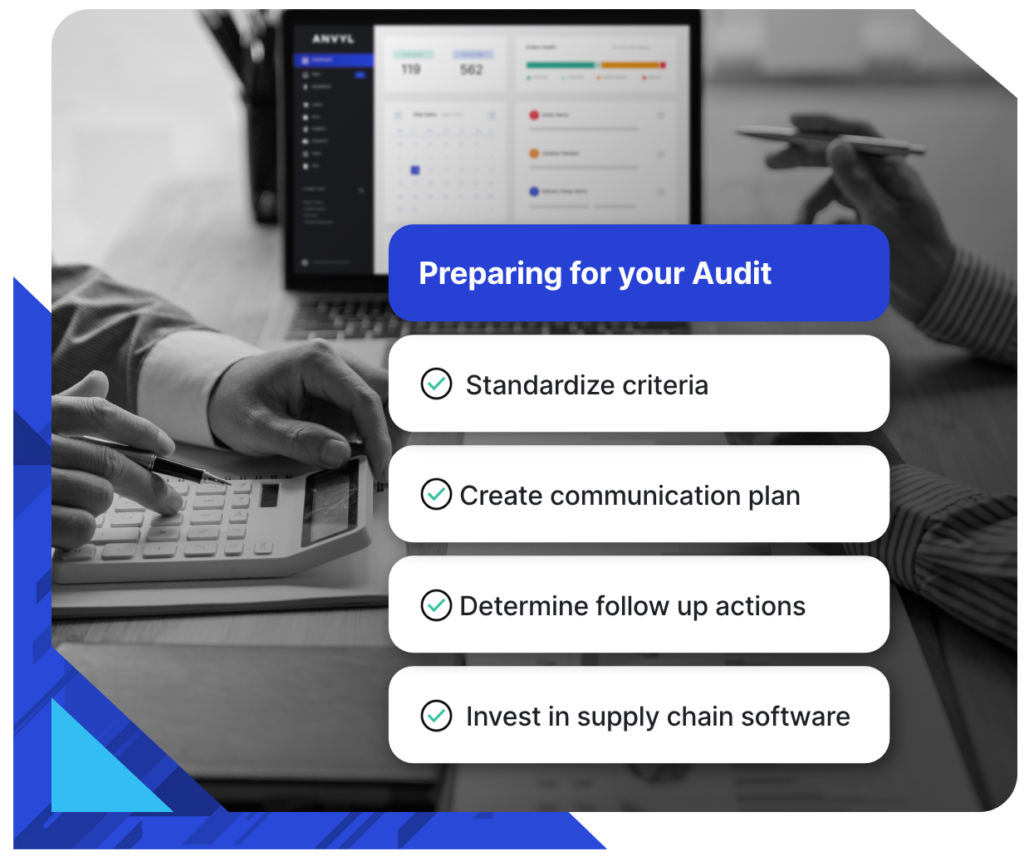
Plan Your Audit
Have a strict plan in place before beginning the audit. This ensures that all auditors have the same guidelines and rules before starting.
Standardize Criteria
The information gathered during the audit must be examined and evaluated thoroughly. All auditors should have standardized criteria to compare findings against to avoid confusion and keep data organized.
Decide How to Communicate Results
Another step to plan before the audit is how you’ll communicate results internally. There should be a clear and precise way of reporting that gives stakeholders actionable insights and informs them of decisions that need to be made.
Determine How to Follow Up
You’ll also want a plan for the actions following an audit. A clear plan helps ensure that any issues or supply chain inefficiencies uncovered in the audit are corrected, and appropriate measures have been taken to improve operations.
Invest in Supply Chain Software
You must also ensure you have the right tools in place to conduct your audit. Auditing your supply chain without the right software requires a lot of manual work, potentially leading to errors, slowdowns, bottlenecks, and even incomplete audits. Audits are much easier with with the support of supply chain management (SCM) software or supply chain risk management (SCRM) software like Anvyl. These platforms help audit teams:
- Track, review, and expedite transactions with digital documentation
- Maintain a secure record of supply chain data that integrates with an ERP or other records system
- Monitor the movement of products through the supply chain
- Convert data into easily readable reports and findings
How to Conduct an Internal Supply Chain Audit
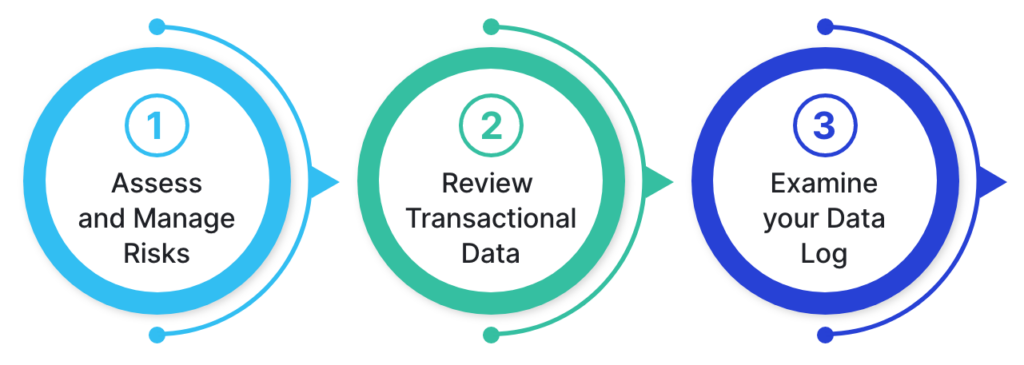
You’re finally ready to audit your supply chain, but you don’t know where to start. Follow these steps to examine your supply chain and evaluate the health of your organization.
Step 1: Assess and Manage Risks
A crucial first step in your supply chain audit is assessing and managing risks. It’s important to understand these risks so you can formulate strategies to manage them. Doing this safeguards your supply chain against disruptions and maintaining consistent operations.
Risks to account for include:
- Brand reputation: Your reputation depends on how consumers look at your practices and deem them as acceptable or questionable. If, for example, a portion of your consumers believe your practices to be unethical, you risk damaging your reputation. Keeping things above board and being transparent in your practices helps mitigate reputational damage.
- Pricing: Pricing refers to the market prices of your goods. This can change when the price of materials changes or your expenses rise. In fact, recent Anvyl research shows that the cost of goods has risen between 5 and 20% for nearly two-thirds of brands. Price increases can affect the flow of your supply chain if raw material cost increases force you to up the price of your products, thus making them less desirable to consumers. Making sure you’re getting the best deal can help mitigate these pricing risks.
- Cybersecurity: Cybersecurity is essential, as it’s an emerging risk for manufacturers. As software attacks on the supply chain become more frequent, you need to review your cybersecurity processes and create systems that protect your valuable data. This can help you avoid undue cybersecurity risks.
- Geopolitics: The global supply chain relies on compliance between different regions and geopolitical areas. However, when there are global conflicts like the war in Ukraine, it can affect the tariffs and trade agreements between nations. Diversifying suppliers in different regions can help you avoid geopolitical risks. According to Anvyl research, this is a strategy most brands use today. 71% of surveyed brands say they have multiple suppliers for the same item, and nearly a fifth (18%) say they do this to reduce the impact of geopolitical tensions.
- Inventory Management: Another area of risk is inventory management. When a business doesn’t transport or store inventory correctly, it can lead to inventory waste or inventory shortages. Having undamaged stock and inventory is key to success. A purchase order (PO) management system like Anvyl can help you maintain accurate inventory through data-driven demand forecasts and enhanced supplier collaboration.
- Contract Management: The contracts that you have with suppliers can also affect your supply chain. For example, if one department owns contracts but does not oversee performance, it can lead to unintentional contract breaches. Keeping people trained and in compliance with agreements can mitigate contract management risks.
- Quality: The quality of goods received also plays a part in your supply chain. Damaged goods or poor-quality materials can derail operations. Having quality assurance procedures in place can help keep you and your supplier at a high standard and avoid any quality control issues.
- Transportation: Choosing a transportation method is a decision that can significantly impact the efficiency and cost-effectiveness of your supply chain. Your choice of transportation method affects lead times, inventory levels, and overall operational agility. Whether it’s by land, sea, air, or a combination thereof, each option comes with its own set of advantages, costs, and potential risks. Your supply chain audit must thoroughly weigh the advantages and disadvantages of each method.
- Legal: Your business can suffer if your suppliers engage in illegal activity, even if you are unaware of it. Improving your contracts and creating rules and regulations for suppliers to follow keeps you compliant and avoids legal risks.
Step 2: Review and Cross-Reference Transactional Data
The next step of your audit is to review and cross-reference your transactional data. This helps ensure that there are no errors or discrepancies across your documents and data. It also ensures that there are no conflicts with the quality, number, or price of goods.
Information that your audit should cross-reference includes:
- Receipts and purchase orders
- Receipts and shipping notices
- Receipts and QA reports
- Invoices and QA reports
- Shipping notices and purchase orders
Step 3: Examine Your Data Log
The final step in your internal audit is to examine your data log. The data log keeps track of all of the information that your team members log. Your auditors need to know who changes data, how data is altered, and where in your organization these changes happen.
Team members might change data for innocuous reasons like correcting an error. However, suppliers can also make fraudulent changes, including raising the price of an item to create a false purchase order, then sending that order to you, and lowering the price again so that you are unaware of the changes.
To examine your data log, you’ll likely need to gather data from various sources within your supply chain including including procurement, production, inventory, transportation, and distribution. This might involve pulling data from enterprise resource planning (ERP) systems, warehouse management systems (WMS), transportation management systems (TMS), and more. You’ll need to consolidate this data into a centralized platform for analysis.
If you use a platform like Anvyl, however, your data will already be centralized in our system meaning you won’t have to shuffle between emails, spreadsheets, and other tools. Hooray! We can also turn this into a report for you, giving you a dynamic snapshot of all supply chain data important to your audit.
Streamlining Supply Chain Audits With Anvyl
Conducting regular internal supply chain audits is imperative for a successful supply chain strategy. Just as your annual health check helps maintain your well-being, a supply chain audit helps identify areas where you supply chain needs support or where operations aren’t functioning optimally.
Anvyl’s intelligent PO management platform makes conducting supply chain audits much easier. We help you streamline the audit process by giving you immediate access to accurate, real-time supply chain data. We’re proud to act as our customers’ single source of truth for their supply chain, enabling them to boost supply chain efficiency, visibility, and supplier collaboration from one central location.
Now that you know how to conduct an internal supply chain audit, contact our team today to learn more about how our platform empowers supply chain excellence.
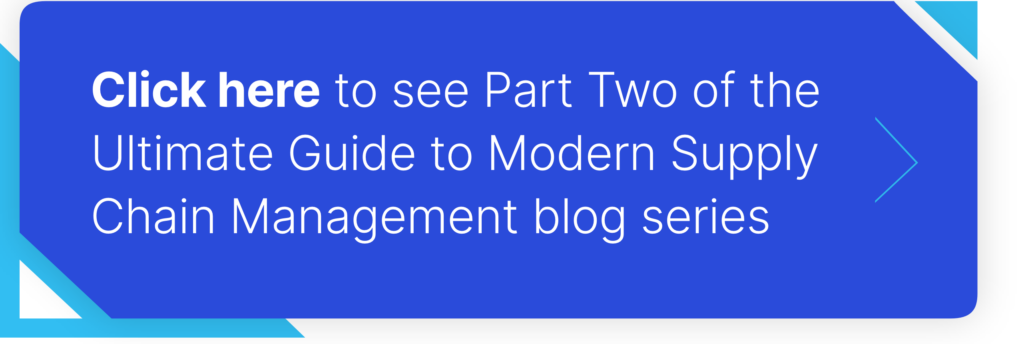