While every supply chain is different, the tasks needed to get through your production process will likely start to repeat themselves as the same parts are ordered with the same suppliers. To create efficiencies within your process, try breaking out the process into different milestones and create a standardized checklist of tasks that both internal and external team members can easily follow. Here is an example below

Let’s explore different milestones and tasks you may wish to track based on the industry you service.
Key Milestones
When purchase orders are placed, there are typically some milestones that every order will go through. For example, you may wish to always track milestones like Pre-Production, Production, Pre-Shipment, Shipment, and Delivery.

During each of these milestones, you may have a separate set of tasks that you and your suppliers need to complete. Below are a few examples of various types of tasks that you may find yourself repeatedly using.
Pre-Production Tasks for Personal Care Products
For personal care brands, it is not uncommon to confirm both colors and samples before production kicks off. For example, the color matching could vary between suppliers and even machines, so it’s important to confirm the colors that will be used on the packaging before production starts. In addition, if any new tooling is needed for the primary packaging, you’ll want to factor that into your planning and ensure everyone who is involved in the approval process is aware of the new timelines.
Below is an example of how you can set up pre-production tasks when issuing orders for personal care products.
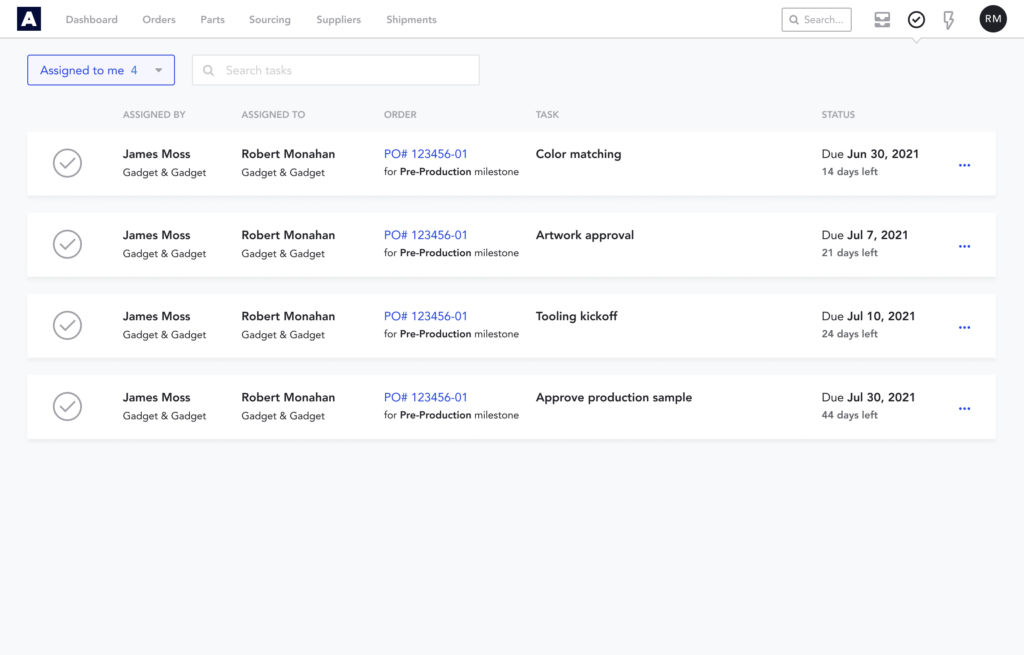
Production Tasks for Cut and Sew Goods
If your brand makes apparel items or other home goods that use fabric, there can be several WIP tasks that you might want to track during production. In this scenario, we recommend setting up a production tracker that assigns out every task, the desired check points, and details for your team and suppliers to help them execute. When suppliers are informed of expectations up front, you reduce the risk of production issues down the line.
Below is an example of how you can set up production tasks when issuing orders for cut and sew products.
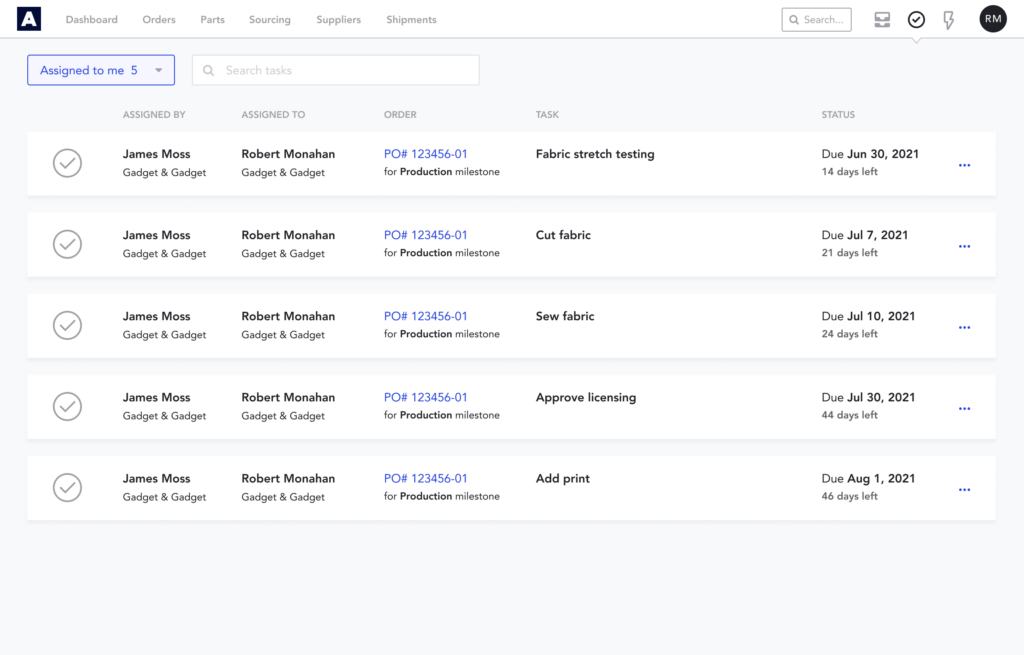
Pre-Shipment Tasks for Food or Beverage Products
Food and beverage goods require a higher level of regulation and quality control before they leave the factory. If your brand sells edible products, ensure that your production process to check the finished goods is efficient by requiring the appropriate documentation for every order. For example, you may wish to request certificates of authenticity, quality release forms, and/or third-party testing documents from the supplier before you move the goods into the Shipment milestone.
Below is an example of how you can set up pre-shipment tasks when issuing orders for food and beverage products.
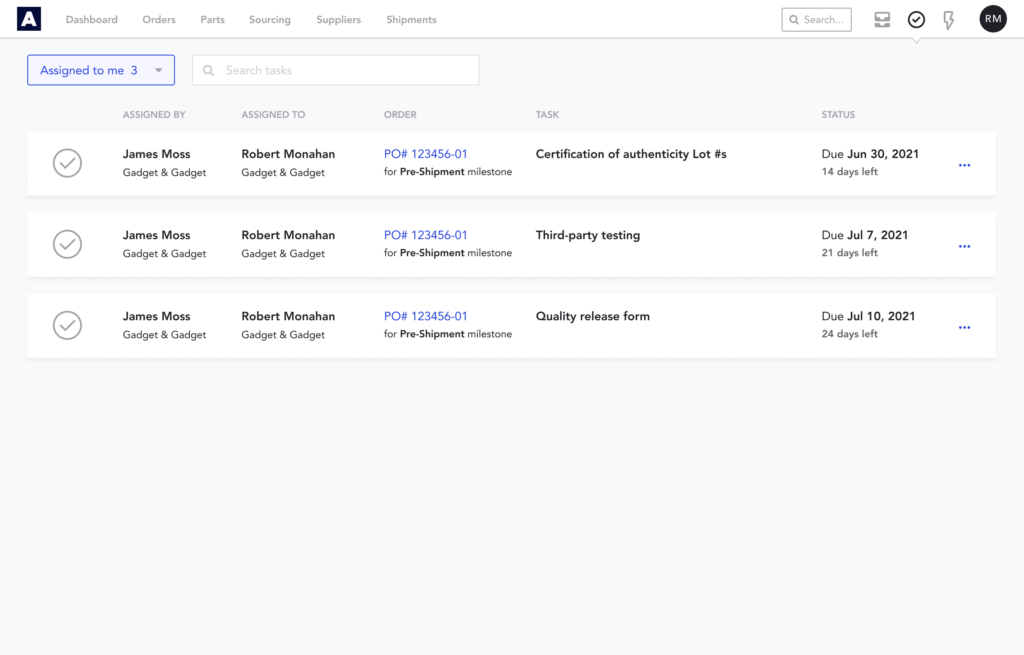
Try Automating Your Operations
We are excited to announce that Anvyl supports automated project management for any tasks you need to track in your supply chain. In addition to our pre-built milestones and automated check-ins with suppliers, this latest enhancement lets customers track specific tasks throughout the order lifecycle and production process by simply linking the task to a milestone. To learn more about how you can set this workflow up, request a demo today.