While changes in your supply chain are inevitable, there are some small adjustments you can make within your operation to reduce recurring delays with your purchase orders (PO). When unexpected issues arise, perform a retrospective with the appropriate stakeholders like your finance team, designer, product manager, and/or suppliers to shed light on inefficiencies in your process and drive improvements to the standard operating procedures (SOP).
Of course, it wouldn’t be scalable to do a retro for every order, so you may be wondering, where do you start? There is one supply chain report you need before initiating these conversations with your supply chain counterparts.
Assess On-Time Performance
Whether you track your orders in a spreadsheet or a cloud-based platform like Anvyl, you should always assess the on-time performance for each order you place with the various suppliers you work with. As you place more orders with suppliers, you will be able to create a report that spots trends and gaps in the on-time performance. For example, the on-time performance report in Anvyl looks something like this:
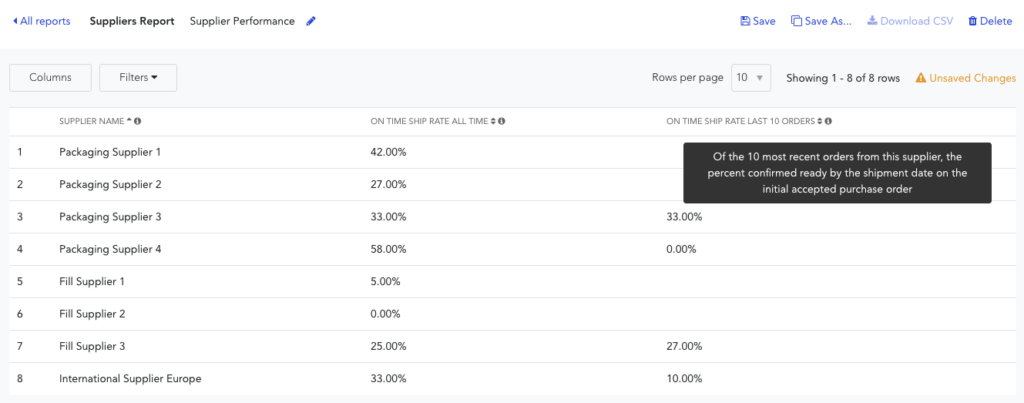
Diagnose the Causes
Once you have this supply chain report at your fingertips, you can set up your retro meetings with the appropriate stakeholders for that month’s or that quarter’s order delays. As an example, we looked at orders delays from 2020, and diagnosed these as top 5 supply chain delays.
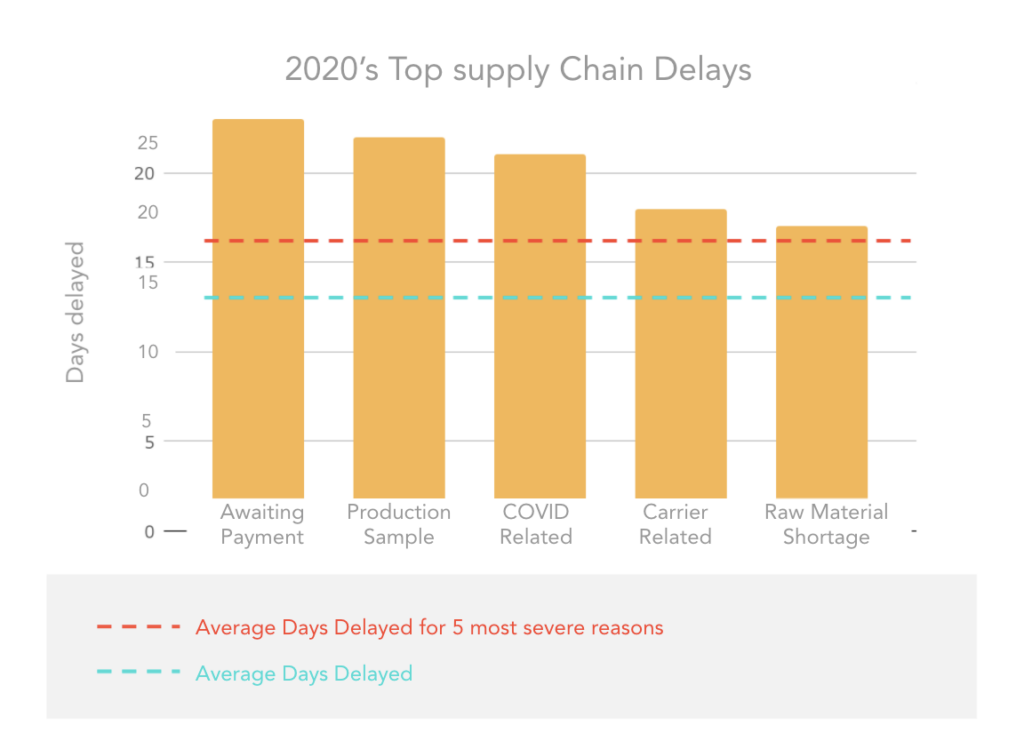
As you have these diagnosis conversations, take the time to understand what is important to your supplier or internal team. Showing empathy towards their process, and working towards a solution that will accommodate both sides towards a favorable outcome will create a better working relationship, and also a more efficient supply chain.
Create an Action Plan to Prevent Further Delays
Since you are assessing past order delays with this report, there’s nothing you can do to undo the delay. (If only time travel existed!) Moving forward, enforcing a revised SOP for your team and suppliers to follow is critical to preventing future delays. For example, if you are having issues with late payments causing production delays, create pre-built tasks for every invoice you receive, and hold your team accountable with a due date.
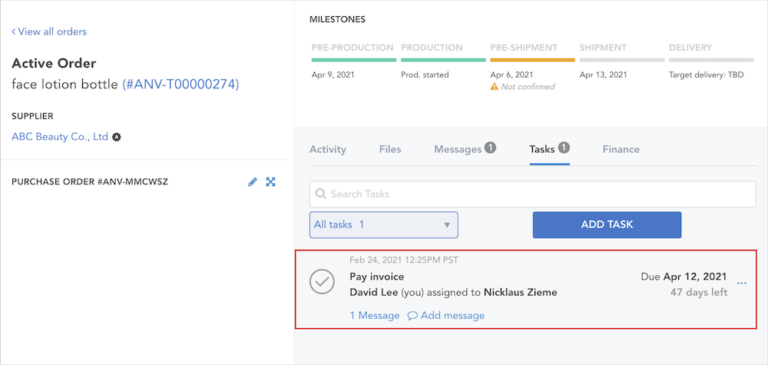
Actioning against your new processes, reminding team members to complete their tasks, and holding your team accountable will result in a more desirable outcome in the future. And, once the SOP becomes second nature, you can focus on other supply chain opportunities that will allow you to scale.
Get Started
If running an on-time performance report seems too daunting and time-consuming, your supply chain will be at risk for even more delays. Learn how this templated supply chain report can be pulled on Anvyl within seconds by speaking with one of our supply chain specialists.